A new carpet has been laid at Carlyle’s House, Chelsea in one of the largest re-display projects at the property since the mid-1970s.
The following has been republished with permission from the National Trust’s Spring 2020 Art, Buildings and Collection bulletin.
By Mo Mant, Co-founder of the Living Looms Project and Penelope Hines, National Trust, Curator, London and South East
The National Trust has been working with historic carpet consultant David Luckham for over 40 years and in 2005 he was invited to research, commission and create a new carpet for the Front Parlour, Drawing Room and China Closet of the house. Working with the National Trust, he was tasked with finding a design, method and materials appropriate to this significant Victorian interior.
A Victorian power couple
Carlyle’s House, Chelsea, opened in 1895 as a literary shrine to Thomas Carlyle (1795–1881), the influential Victorian essayist, philosopher, satirical writer and historian who lived in the house for 47 years. Since 1936 the property has been in the care of the National Trust, which has more recently endeavoured to give equal prominence to Jane Welsh Carlyle (1801–66), Thomas’s wife, who is now admired for the witty and uncompromising letters in which she recorded her social and daily life. The couple’s letters provide unique insights into the lives of an extraordinary couple and their little home in Chelsea, where they were visited by many of the most famous literary figures of the day, including Charles Dickens, Alfred Lord Tennyson, the Brownings, William Makepeace Thackeray, Anthony Trollope, John Stuart Mill and John Ruskin.
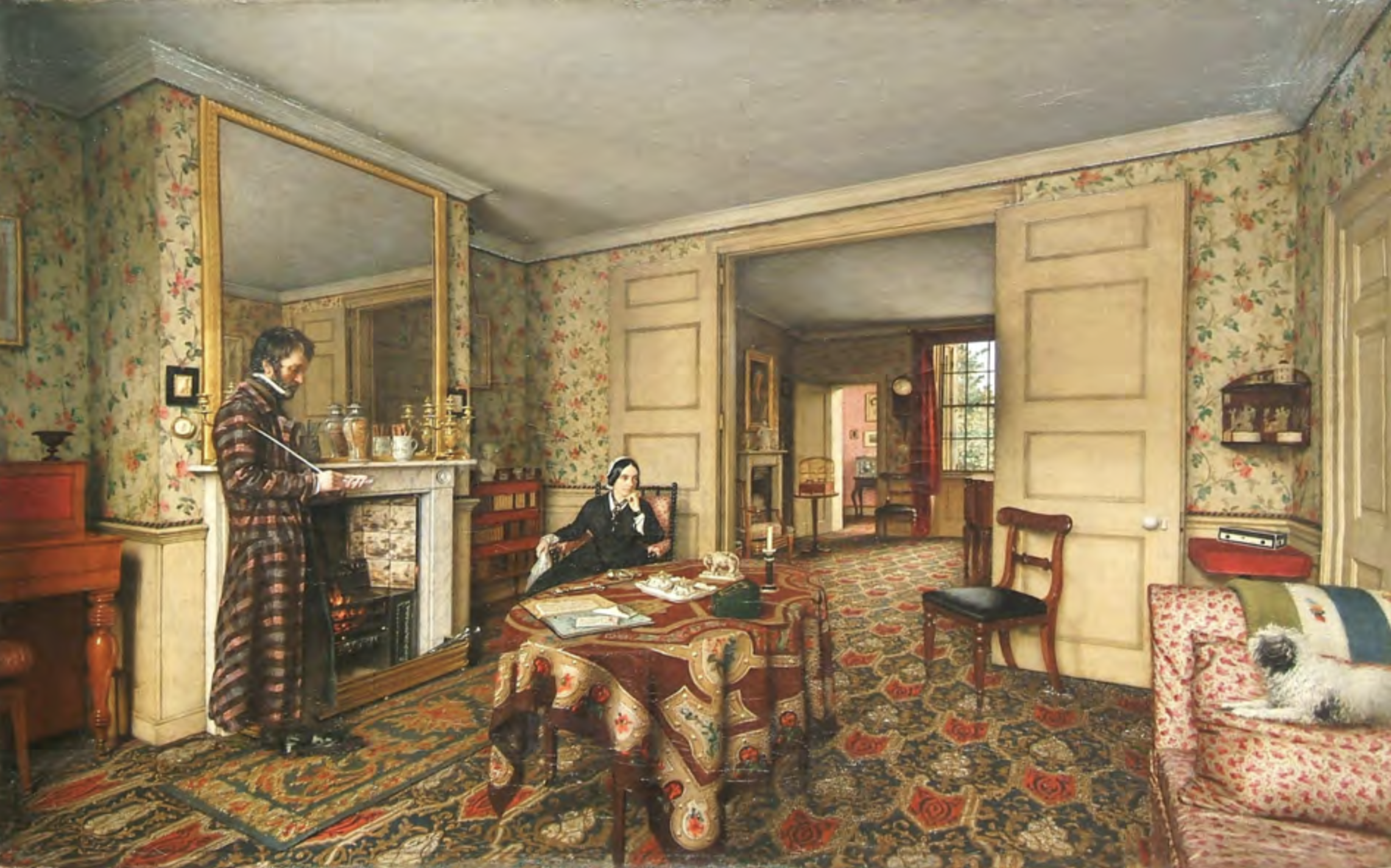
Fig. 1: A Chelsea Interior, 1857–58, Robert Scott Tait (1816–97), oil on canvas, 86 x 114cm, ©National Trust Images/Geff Skippings
Reconstructing a home
Carlyle’s House was built in 1708 and retains many authentic features from the Carlyles’ residency, including the soundproof attic that Thomas Carlyle had built in 1853 so that he could work in peace and quiet. The house also contains many pieces of furniture, books, pictures and other artefacts that belonged to the Carlyles and which have been returned to the house over time.
The interiors of the house are recorded in Jane’s letters, in drawings by Helen Allingham and, of most significance for the new carpet, in the painting A Chelsea Interior by Robert Tait (1816–97) (Fig. 1). Tait exhibited the painting under this anonymous title at the Royal Academy in 1858, but many would have recognised the celebrity couple in it and their dog, Nero. The painting was bought by William Bingham Baring (1799– 1864), second Baron Ashburton, the husband of one of Carlyle’s greatest female admirers, Louise Stewart-Mackenzie, Lady Ashburton. It was acquired by the National Trust from the seventh Marquess of Northampton in 1998 with the help of the Art Fund and an anonymous benefactor.
In an often-quoted letter, Jane Carlyle wrote of A Chelsea Interior:
My chief impediment has been that weary Artist who took the bright idea last spring that he would make a picture of our sitting room – to be ‘amazingly interesting to Posterity a hundred years hence’.
She would have been surprised, when scathingly quoting Tait, to learn just how interesting the painting has now become as an invaluable record of the room’s design and décor.
In the 1950s a new curatorial approach to the house began to develop that sought to present it as a facsimile of the Carlyles’ home rather than as a museum of associated objects, as had been the case when the house was cared for by the Carlyle House Memorial Trust and during the early period of the National Trust’s ownership. In the 1970s the interiors of the Front Parlour and Drawing Room were reconstructed, guided by their appearance in A Chelsea Interior and under the direction of Martin Drury, then the Trust’s Historic Buildings Representative and later its Director General.
This reconstruction included pieces of furniture formerly owned by the Carlyles, either acquired by the National Trust or generously on loan, as well as new objects similar to those owned by the Carlyles, including textiles and wallpapers sourced from the commercial market. These were aesthetically comparable to their equivalents seen in A Chelsea Interior, but were included in order to recreate the atmosphere of the period rather than to replicate the rooms exactly.
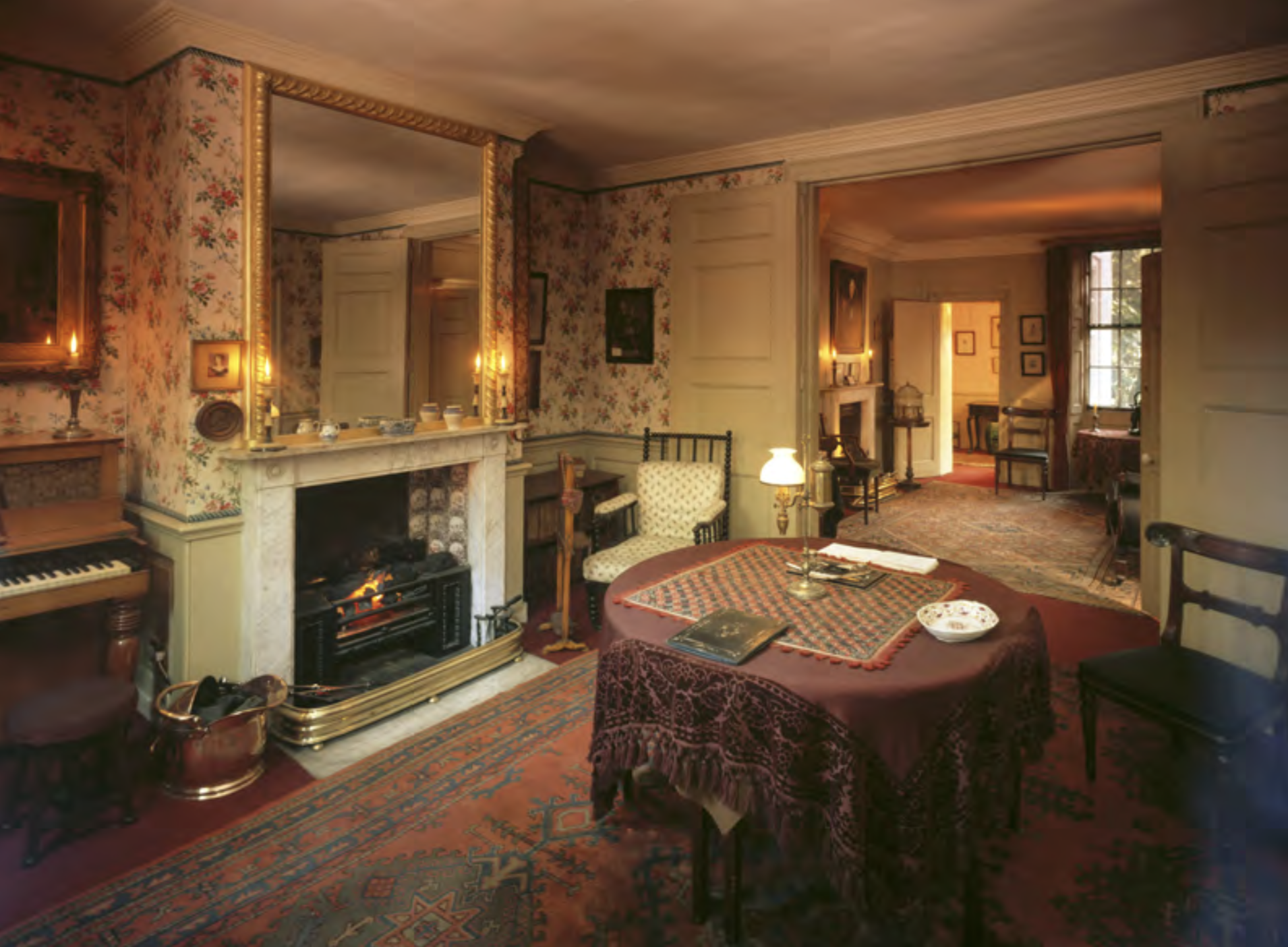
Fig. 2: The Interior of Carlyle’s House before the new carpet was installed, ©National Trust Images/Matthew Hollow
Floor coverings
In the 1970s the rooms were carpeted with thick red felt underlay overlaid with patterned Turkish-style carpets (Fig. 2). Over time the ‘Turkish’ carpets became worn, and there has long been a desire for a floor covering across the three rooms that is more authentic in both material and appearance.
A number of specialists were drawn together to consult on the project. As already mentioned, consultation started in 2005 with David Luckham, who contributed his knowledge of the history of carpet styles, colours and manufacturing processes. He had worked on durable, historically informed carpets at other National Trust properties, including Oxburgh Hall and Felbrigg Hall, both in Norfolk. At Oxburgh, David created a carpet based on a 19th-century sample of English ‘Brussels’ stair carpet. To allow full public access to the Library at Felbrigg Hall, the National Trust also worked with him to commission a 34-colour, worsted wool representation of an 1840s printed tapestry carpet (NT 1402098).
One of the challenges encountered at Felbrigg is a familiar one for those who work with historic textiles – the original technology and skills had been lost. With his colleague, Mo Mant, David founded the Living Looms Project in 2006 in an effort to halt this trend. Living Looms conserves and promotes the knowledge, skills and technologies associated with traditional textiles. The Carlyle’s House commission supported the preservation of the project’s fine Axminster looms.
There were several factors to consider in the design and production of the new Carlyle’s House carpet: the appearance of the original carpet in the painting, the realistic capabilities of the 19th-century looms used to produce it, and the likely detail of the pattern based on historical evidence. Additionally, one of the joys of Carlyle’s House is that visitors are free to roam the house as one would a private home, so the carpet needed to be sufficiently hard-wearing to allow this.
It soon became apparent that to meet these stringent and varied requirements, a bespoke carpet would need to be designed and produced using traditional methods. David Luckham commissioned artist Roger Sullivan to design the Carlyle’s House replica carpet and Grosvenor Wilton to weave it.
He worked closely with them throughout the process to supervise the design, specification, colour selection, manufacture and – later, with the fitters – the installation of the carpet.
Pattern and colour
The process of interpreting the pattern and colours of the carpet from A Chelsea Interior had to begin with advice from curators and conservators.
A distinctive pattern is clearly shown in the painting but its rendering of the room in perspective causes the proportions of the pattern to broaden and condense. This is particularly evident in the lower left-hand corner of the painting, where the pattern has been ‘stretched’. Fortunately, the actual scale of the pattern in the painting could be examined in relation to the furniture depicted, some of which remains in the room, and by studying historical examples.
The colour scheme of the carpet was another important consideration: analysis of the painting established that where the paint now appears tinged with blue it would originally have had a more vibrant green tone. As with the scale of the pattern, an informed decision was made about the colour scheme using a combination of research expertise. The fine detail of the carpet, including the gold borders of the shield and the scrolling foliage, which are only shown in a few instances in the painting, are picked out in tonal shades and bring a depth to the design and composition that the new carpet needed to emulate.
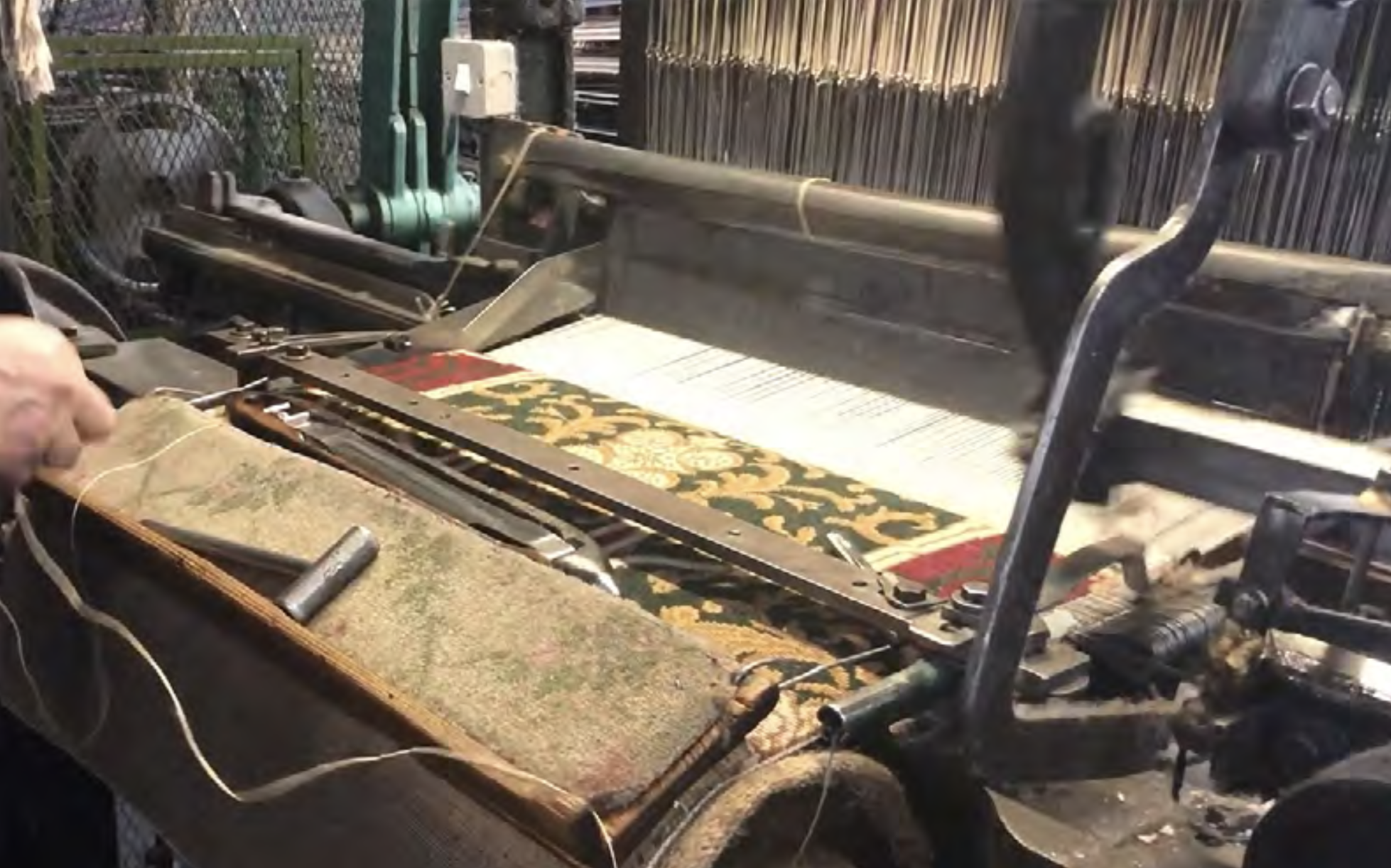
Fig. 3: The new Carlyle’s House carpet on the loom, ©Woodward Grosvenor Ltd
From design to installation
While National Trust curatorial staff were researching and working to create the best possible reproduction and presentation, the design artist, the staff of Grosvenor Wilton, the Living Looms Project, the dyers and the installers, Edgeco Ltd, were focusing on the design, production and installation elements of the project.
The carpet was identified from the painting as a fitted Wilton carpet by a process of elimination. In 1857 three main types of carpet were being produced that were suitable for wall-to-wall fitting: Chenille Axminster, Wilton/Brussels, and Kidderminster flatweave (or ‘ingrain’). In this context, Chenille was unlikely because it was usually reserved for state rooms and other formal spaces. The original carpet’s repetitive pattern also made this option unlikely. Flatweave carpet, like Wilton and Brussels, is woven in narrow widths that are then sewn together, and all are characterised by a repetitive pattern. They also have a limited colour distribution but the pattern colour yarns of flatweave carpets are introduced via the weft of the textile and this is visible in the pattern style of the finished carpet. In velvet Wilton and Brussels carpets, however, the coloured pattern yarns are introduced via the warp threads, often selected by a Jacquard mechanism above the loom (see text box, below), and this characteristic is also visible in the finished carpet. It was therefore determined that the original carpet was a Brussels Wilton. Finally, evidence relating to the financial status of the Carlyles also suggests that, since they were not wealthy, they would probably have chosen the most economical type of Wilton carpet – Brussels Wilton. Fortunately, this option also fitted very well with the public- use purpose of the new carpet.
The Jacquard mechanism
In loom weaving, a thread called the weft is interlaced at right angles through a set of threads called the warp. Patterned fabric is created by regulating the order in which the weft passes over and under the warp threads. Traditionally, this was slow and highly skilled work, carried out by master weavers and their assistants (or ‘draw boys’), and the product was therefore relatively expensive. In 1804, however, the French weaver and merchant Joseph-Marie Jacquard (1752–1834) patented a revolutionary loom that used interchangeable punch cards to determine the pattern. It allowed complex patterns to be produced more quickly and accurately bringing down the cost of patterned fabrics and making them more widely accessible.
The process begins with a designer painting the selected pattern onto squared paper. The pattern is then translated by the card-maker onto the punch cards, each of which represents a different part of the pattern. Each unpainted square on the paper is marked by punching a hole in the card. The punched cards are then laced together and fed into the Jacquard mechanism on the loom. This incorporates a series of sprung pins that either pass through the punched holes, activating hooks to raise the selected warp threads, or are blocked by an unpunched area of card, leaving other threads untouched. The shuttle then passes the weft thread under the raised warp threads and over the others, creating the ‘pre-programmed’ pattern as it goes.
Brussels carpet-weaving in England, is believed to have begun in the late 17th century. Brussels carpets are woven in narrow widths on the loom. Writing in 1838 (19 years before the painting of A Chelsea Interior) for the British Cyclopedia of the Arts and Sciences, Charles Partington explained:
‘Brussels’ carpets are not made in large squares, but in pieces about seven eighths [17 inches] wide … When well-made they are very durable, and being at the same time elegant, they are at present much in request for the good apartments.
The working design was painted by Roger Sullivan, who has 50 years’ experience in this field and also painted the design for the National Trust’s Felbrigg Hall Library carpet. Roger then transferred the painting to a computer for colour conformation, Jacquard card preparation and to calculate the amount of yarn required for each colour. The chosen yarn colours were then checked several times against the painting, the known mid-19th-century colour palette, and the colours’ compatibility with each other and with the existing colours in the rooms in which the carpet was to be fitted. Once the colours had been agreed, sufficient worsted woollen yarn was purchased and sent to the dyers in
Yorkshire with the chosen yarn samples and instructions to ‘dye to side’ or ‘dye to cut’ (although the colour remains the same with either option, each one results in a tonal difference created by the effect of light falling on the different surfaces). While the yarn was being dyed, checked and wound onto spools, the punched Jacquard pattern cards were being produced by Grosvenor Wilton. The Jacquard mechanism was set up with the cards over the loom and the loom made ready to receive the yarn (Fig. 3). The spools and trays of yarn were then set up and weaving commenced. Once weaving was complete, the carpet was thoroughly checked and a thin latex backing was applied.
At Carlyle’s House there were extended discussions about the use of felt under the carpet because felt or padding can produce a luxurious feel for what was (historically) a less expensive type of carpet. However, the team also had to consider contemporary conservation needs and the risk that the felt and wool could attract pests.
It was determined that the best preventive conservation method was good housekeeping and eventually a 42-ounce hair felt was chosen, crosslined with Feltine paper.
The last stage of the carpet-making process was to hand-stitch the lengths of carpet together width-wise into a ‘blanket’ to roughly fit the room. This was then delivered to the property and installed over the course of two days using the traditional ‘turn and tack’ method. Prior to this, the ornaments, books, soft furnishings and small pieces of furniture had been moved out into other rooms. The large pieces of furniture were too heavy to move far, so the carpet-layers were required to work around them while property staff moved the pieces around the carpet.
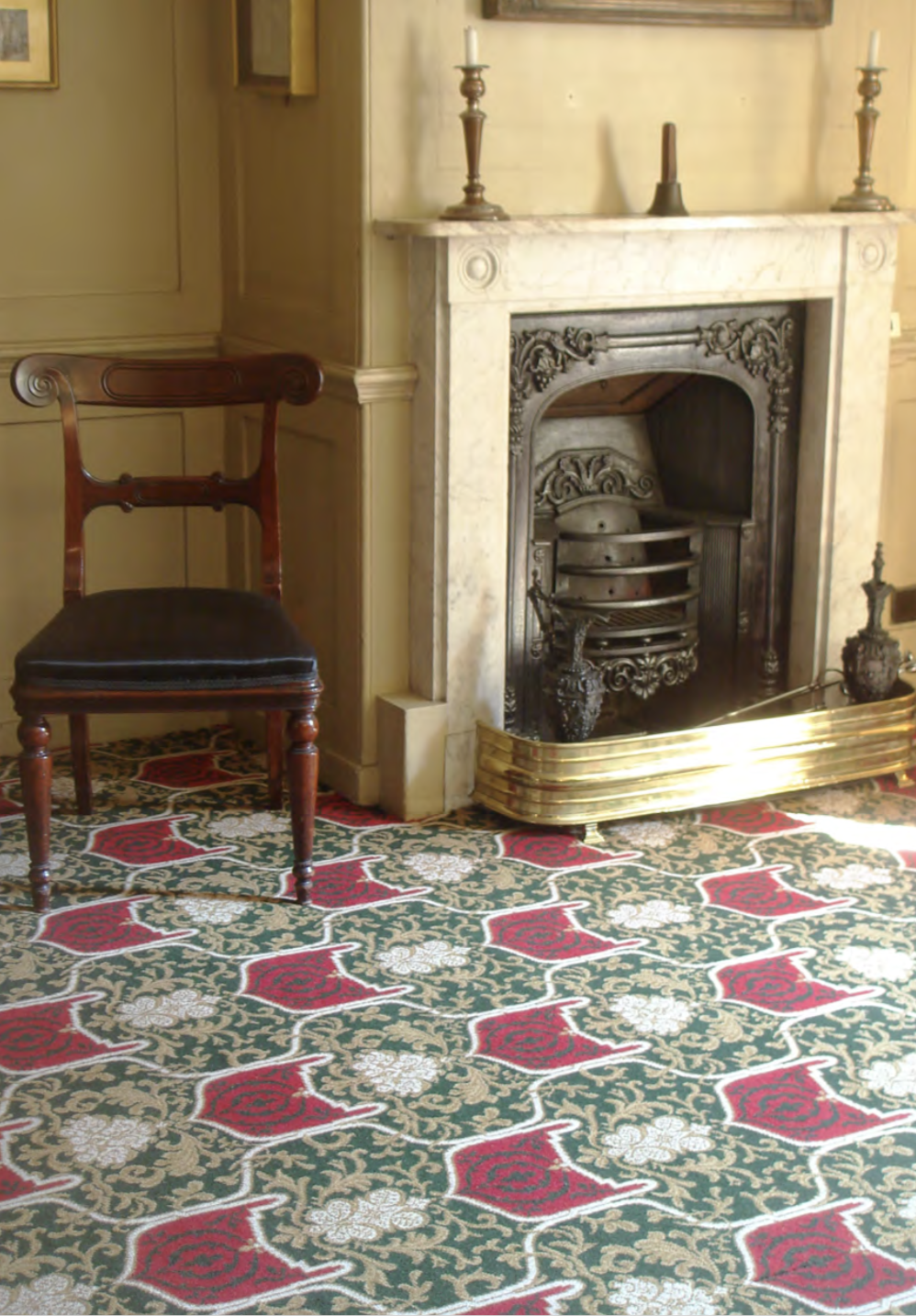
Fig. 4: The new carpet installed, ©National Trust Images/Jonathan Marsh
Visitors’ views
Visitors have responded very positively to the new carpet (Fig. 4). Its appearance and quality are often admired but, perhaps more importantly, visitors often comment that ‘it looks like it belongs’. Rather than being jarringly new in a Victorian room, the carpet seems to elevate the patterns on the walls, furnishings and ceramics, and ties together the entire aesthetic of the room. The success of this effect is, without doubt, due to the intensive research and expertise that were brought to bear on the project by the custodian, the house steward and other property staff, David Luckham and the Living Looms Project, the installers, and property curators past and present.
Traditional skills and technologies
Off-setting the success of the project at Carlyle’s House, however, is a wider context of disappearing traditional carpet-making skills and technology. The level of authenticity achieved at Carlyle’s House will no longer be available to curators unless urgent action is taken to safeguard the historic looms and skills that are uniquely able to produce the best historic carpets. Chenille and printed- tapestry looms no longer exist and the last few of the highest quality spool Axminster and Wilton looms are dangerously close to being lost. Without authentic, high-quality carpets, historic rooms and collections will be impoverished.
More information about the not-for-profit Living Looms Project can be found online at http://thelivinglooms.co.uk